The Importance of Design Details and Workmanship in Construction
- Benny Kuriakose
- Jul 28, 2021
- 6 min read
Updated: Mar 24, 2022
The biggest challenge that the building construction industry in India facing today is to ensure good quality control procedures in construction. The durability of buildings is highly dependent on the quality of workmanship in construction and the design details. Many of the modern buildings have maintenance problems. It is not because Reinforced Cement Concrete was used, but the way in which it was handled during the construction. The quality of building construction work and the attention to building details assume great importance in India, where standards and specifications are not strictly followed in the residential building construction scene. The quality of workmanship has come down drastically during the last two decades. Waterproofing the toilets or waterproofing the RCC roof was not at all common when I started practice twenty years ago. Now it has become the order of the day. Using these construction materials as a shortcut to good workmanship is not at all right for the durability of materials and the buildings.
Table Of Contents
Thinking Durability: Why is Durability of Buildings Important?
Among building construction materials, only mortar increases in strength over time. A building exposed to the elements of weather is constantly decaying. Every building material has a definite life. For example, roofs with coconut thatch last for one year while those with palm thatch last for four years.
Once the minimum quality of the materials is assured, the durability of a structure is dependent on the quality of workmanship and the design details. There is no shortcut to quality workmanship in construction. For example: take the case of plastering, the separation of plaster from backing occurs due to the following reasons:
Water penetration inside the wall, which may be due to plumbing leakage or other reasons.
The finishing coat being stronger than the undercoat.
Lack of suction control during application.
The excessive thickness of coats.
Inadequate raking out the joints.

Of the above, the last four are controlled by the mason at the site. In the final analysis, flaking of plaster is because of inadequate understanding of the procedures to be followed. In other words, it is because of poor workmanship. The greater concern is that a building with poor workmanship is not durable.
Thinking Quality: How to Achieve Quality in Construction?
Architecture can be conveyed in words and by architecture drawings, workmanship cannot. "In practice, the designer hopes the workmanship will be good, but the workman decides whether it shall be good or not. On the workman’s decision depends a great part of the quality of our environment." (David Pye, The Nature and Art of Workmanship)
The engineer or architect can point out and correct the major defects of quality of workmanship and materials, but they cannot make bad workers produce good quality workmanship.

Society is accustomed to paying for quantity, not quality. Labor contracts and overtime lead to a reduction in quality. In labour contracts, the labour cheats by reducing the quality. The owner thinks that he has gained because of the apparently increased output. Building owners don’t realize that they are cheated in this manner. The additional cost in attaining quality is actually only marginal, whereas ensuring quality pays off in the long run, in lowered maintenance costs.
Today, there is little incentive for the worker to do quality work. Manual labour is no longer respected. There seem to be only workers, no craftsmen. A craftsman understands the technology of his craft and he can provide leadership to produce good workmanship.
Important Building Details for Quality Construction
Architectural building details play a major role in the durability of the buildings. Unfortunately, many of the traditional standard building details such as roof overhang, coping, etc. which we used to follow in our old buildings are not being followed in contemporary buildings. We have a notion that the traditional building materials are not durable and the durability of concrete structures and other modern buildings is high. Experiences over the years have shown that many of the RCC buildings need repairs of serious nature. Some of the details which are missing in the present-day building construction work are mentioned below:
a. Rising Damp
When damp soil comes into touch with porous walling materials like brick or stone, moisture is pulled into the pores by a physical process known as capillary action. The absorbed moisture will increase within the wall to a point where the rate of evaporation and the rate at which it may be sucked out by capillary forces are balanced. The height will change depending on the soil water table level.
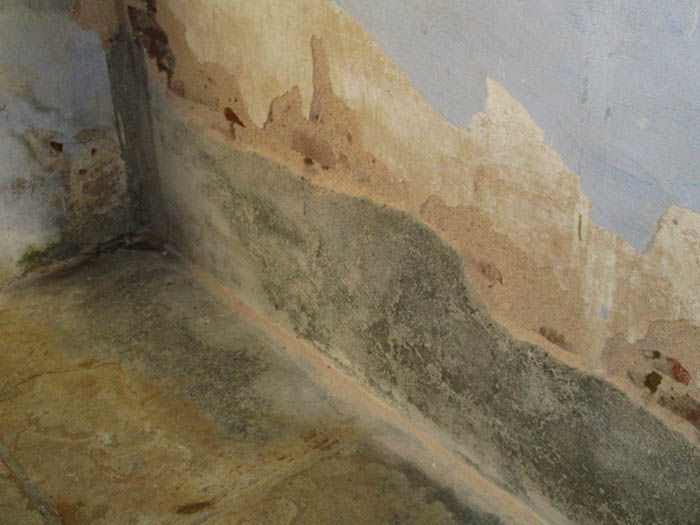
The effects of rising damp usually extend from 3 cm to 100 cm above floor level and exhibit a sharp change from wet to dry on the wall. Moisture will be present throughout the wall thickness. Contaminating salts may be seen as white deposits or crystals.
Salt crystallization is the precipitation of salts such as chlorides, sulphates, and carbonates in the building material. The salts are activated only when a suitable agent is present. Water plays a key role as an agent either in the form of moisture, which causes dampness or subsoil water rise in the structure or percolation; or seepage of water accumulated in the structure due to cracks and crevices. When water is drawn from the soil, it always contains the solution of salts present in the soil.
When evaporation takes place on the surface, the salts get deposited near the surface and the mechanical forces exerted during crystallization cause the plaster or brick to disintegrate over a period of time. Damp-proof courses are strict to be provided in such areas where there are chances of rising damp.

b. Coping
A top is needed for a wall to throw off rainwater and protect the brickwork below from being saturated. This is called coping. Traditional copings have a slight overhang on each side of the wall face with a groove called a throating on the underside. Rainwater drips off the edge without running down the face of the brickwork.
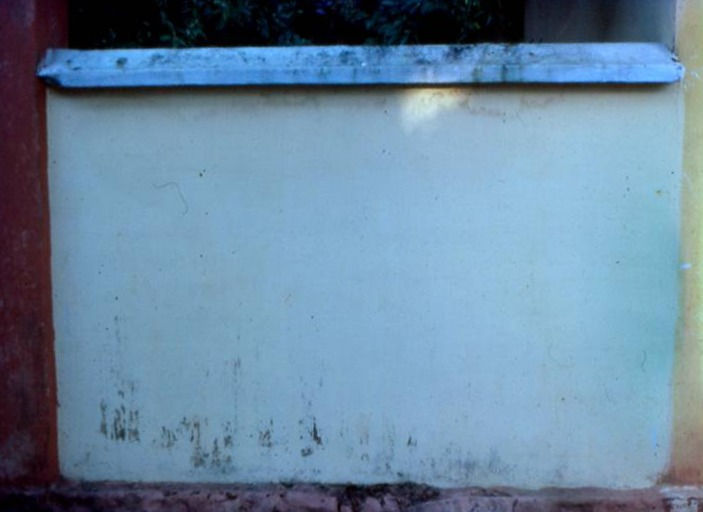

c. Sloping Sunshades
Sunshades should be provided to protect walls, windows, and doors against sun and rain. The sloping sunshade is advisable rather than a flat sunshade because flat sunshades can lead to the dampness of the wall over a period of time.

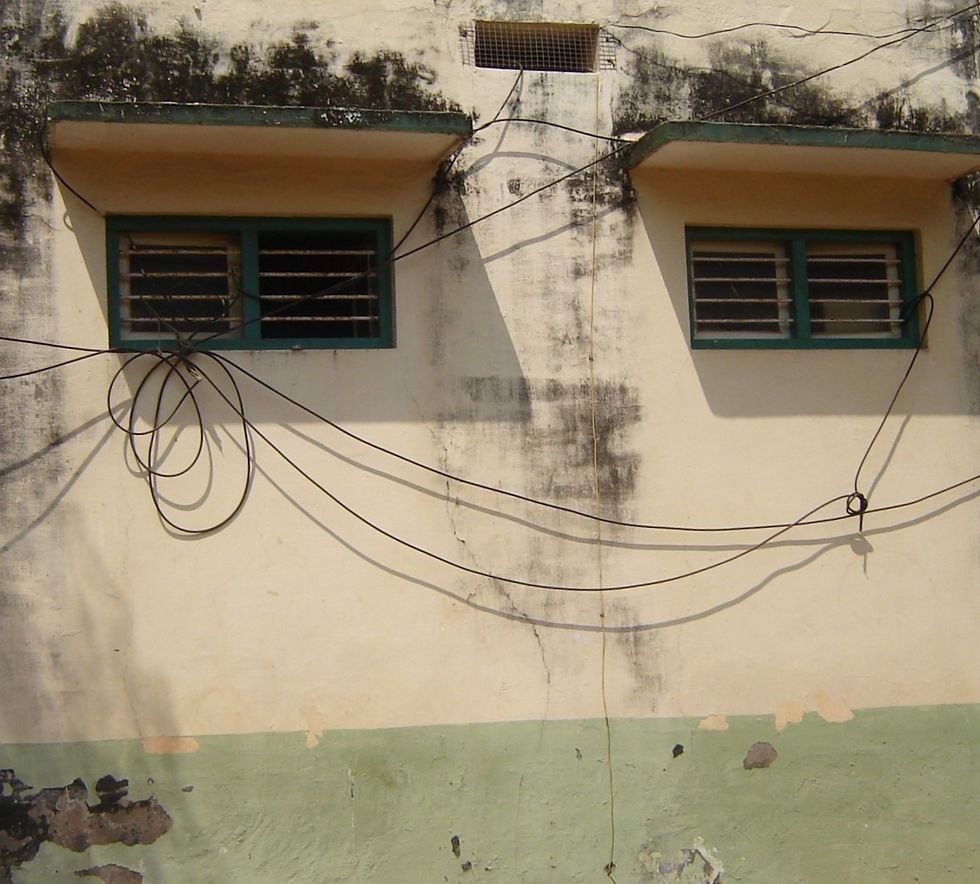

d. Ventilation of the Timber Roof & Floor
In cold climates especially in hill stations, the ventilation of the roof and the timber floor are necessary to avoid the growth of wet rot and dry rot which affect the timber members. Traditionally they were ventilated by giving openings to facilitate air circulation. The absence of these building details for ventilation causes problems to the timber members in many of the buildings.

There are more than two thousand varieties of termites whose identification is a complex and skilled task for scientists. The termite, though often called a white ant, is only very distantly related to the ant, although it is a highly organized community-building species. Its two varieties are soil termites and dry wood termites. The former is ground-nesting and the latter a flying variety.
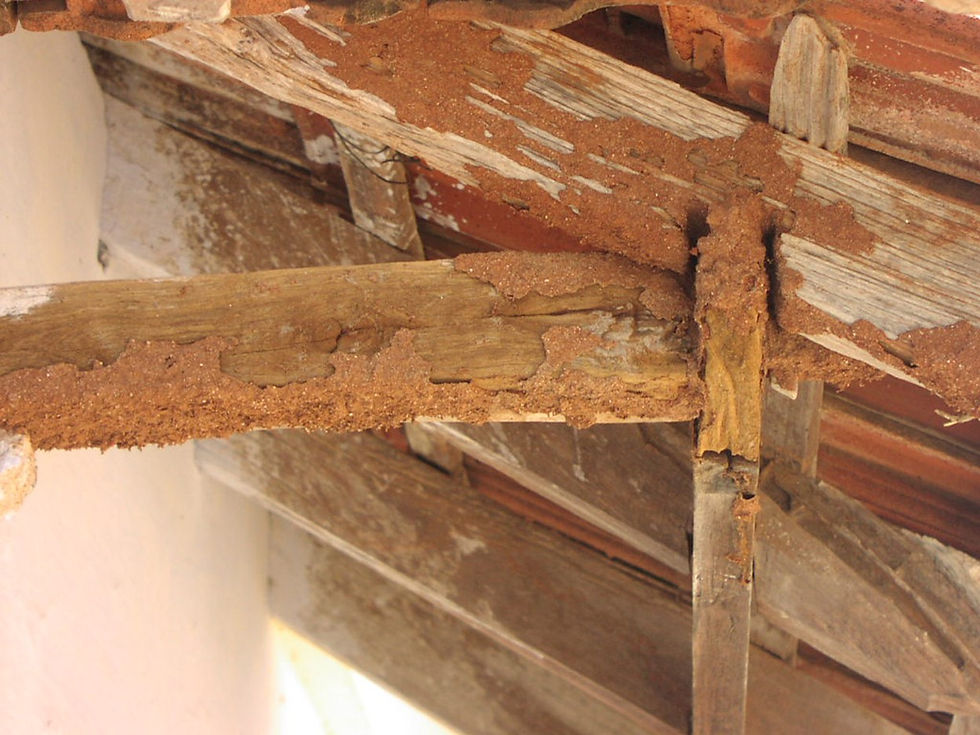
Soil termites are more widespread and they need to maintain contact with the nest in the ground. They can thus be physically barred from the building structure by providing mechanical and chemical barriers during the building construction process. The soil termite shuns light and wherever forced to take a passage along a lighted area will build a tunnel within which it can travel concealed. It cuts the way through the soft mortar or voids to form the tunnels, which carry it from the ground-based colony to the upper levels where timber is plentiful. Soil termites can pass through a 2 mm crack or an expansion joint (eating through the rubber compound) between adjoining concrete on-ground flooring. Soil termites can also travel under parquetry and floor tiles to get to the wall framing timbers. In the process, they may well find food supplies in small organic particles in the mortar, straw, organic dust, etc.
The chemical and mechanical barriers will prevent soil termites from entering the building, but will not prevent attack by dry-wood termites, which are free-flying pests. Infestation by these should be prevented either by using naturally resistant timbers or by pre-treating with timber preservatives.
The pest control treatment done in the foundation will prevent only the soil termites from attacking the timber. Also giving a mechanical barrier using a dense concrete mix increases the durability of the materials than the chemical treatment because the chemicals which are added to the ground get diluted over a period of time.

Every building material has a definite life cycle. Good quality workmanship in building construction works and providing building details such as coping, termite control, sunshades, etc go a long way in ensuring the complete utilization and durability of materials and the building.
Can a Kadappa stone be used instead of the dense concrete mix? Does it still act as a physical barrier to terminates?